Graeme Rice
Additive Manufacturing (AM) describes the process of creating a three-dimensional object by building up a series of successive layers of material(s) over time. This method of manufacture has become increasingly popular across a wide range of industries, and 3D printers are now used by hobbyists at the enthusiast level, and by multinational aerospace and defence contractors. The use of 3D printers in the production of firearms has been extensively documented by ARES, most notably in our 2020 report, Desktop Firearms: Emergent Small Arms Craft Production Technologies. The primary benefits of AM include cost savings, improved supply chain efficiency and improved precision in both internal and external geometries. Objects are first digitally created using Computer Aided Design (CAD) programmes, and are then ‘built-up’ with material added in layers via a variety of processes.
Over the past few years, AM techniques have been increasingly used in the construction of energetic materials, such as propellants, pyrotechnics, and explosives. AM offers significant benefits when applied to the construction of energetic materials, most notably the ability to take a more flexible approach to design and manufacture under time-sensitive (and, potentially in the future, under field) conditions. The use of 3D printing is often able to offer cost savings and a reduction in supply chain complexity, as well. The ability to produce customised geometries allows for the rapid development, prototyping, and production of highly specialised munitions for a variety of specific-scenario uses, including applications in both counter-terrorism and conventional war-fighting—all whilst capitalised on cost saving and supply chain simplification.
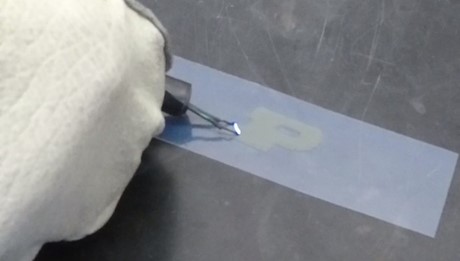
The use of 3D printers, specifically those operating the vibration assisted printing (VAP) technique, can allow for manipulation of the number, size, and shape of voids within the printed materials, allowing the user to change explosive sensitivity—specifically the energy release in the chemical reaction zone—through the manipulation of voids at the mesoscale level within the material. The reduction in porosity leads to improved density of material, producing more consistent thermal tolerances and more predictable behaviour under test conditions. This cannot be done through traditional manufacturing techniques such as casting, which requires the compounds to be mixed imprecisely—leading to additional voids and impurities in the material.
The net result of this offers a range of possible benefits for different usage scenarios. For example, energetics can be designed at the mesoscale level to provide more precise blast effects where collateral damage is of particular concern—such as in requirements to breach entryways in a safe manner, or in airbag deployment—or to provide other specialised charges that have mission-specific limits such as width and weight. Purdue University have conducted significant research to develop 3D-printed energetic materials, and have developed novel techniques in cooperation with entities such as the Defense Systems Information Analysis Center (DSIAC), aimed at applications within the defence industry.
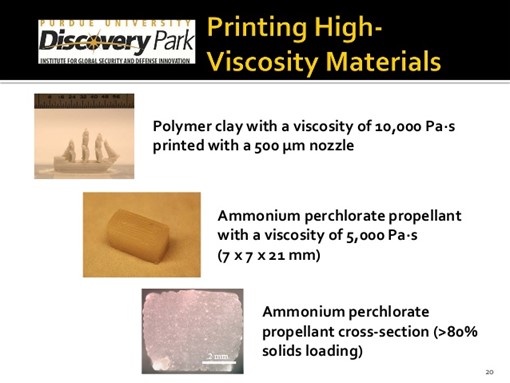
In a DSIAC webinar video posted on 5 May 2021, the application of AM to the construction of solid propellants was examined in detail. Findings presented in this presentation show that AM improves the density of the propellant whilst not having a significant adverse effect on burn rate. Additionally, the benefits of AM in respect of rapid prototyping allowed the use and assessment of different bonding agents during the design-and-evaluation phase of production. Printed propellant using Hydroxyl-terminated polybutadiene(HTPB) and another Illumabond-curable binder demonstrated higher density, together with a reduction in the creation of voids within the final product.
Whilst the technology is still in a nascent stage, its potential is significant. Ultimately, AM will continue to disrupt the energetic materials market and is set to increase in popularity and use cases. Key to this disruption is AM’s ability to be highly scalable and to offer huge benefits for supply chain management whilst also enabling rapid prototyping and deployment, and unparalleled control over initiability, detonation velocity, and mechanical characteristics in the finished product.
References
3D Printing Progress. 2018. ‘3D printer for energetic materials’. Article: <https://www.3dprintingprogress.com/articles/16049/3d-printer-for-energetic-materials>.
Defense Systems Information Analysis Center (DSIAC). 2021. ‘DSIAC Webinar: Additive Manufacturing (AM) of 3-D-Printed Energetic Structures’. YouTube video: 5 May. <https://www.youtube.com/watchv=y6TbXwtW3iw&ab_channel=DefenseSystemsInformationAnalysisCenterDSIAC>.
Fleck, T.J., A.K. Murray, E. Gunduz, S.F. Son, G.T.-C. Chiu & J.F. Rhoads. 2017. ‘Additive manufacturing of multifunctional reactive materials’. Additive Manufacturing, Vol. 17 (October), pp. 176–182.
GE Additive. ‘What is Additive Manufacturing’. <https://www.ge.com/additive/additive-manufacturing>.
Hays, G., Ivan T. & N.R. Jenzen-Jones. Desktop Firearms: Emergent Small Arms Craft Production Technologies. Research Report 8. Perth: Armament Research Services (ARES). <https://armamentresearch.com/wp-content/uploads/2020/03/ARES-Research-Report-8-Desktop-Firearms.pdf>.
Innovation and Partnerships Office. ‘3D Printing of Energetic Materials and Components for Optimized or Enabling Technologies’. <https://ipo.llnl.gov/technologies/chemicals-and-materials/3d-printing-energetic-materials-and-components-optimized-or>.
International Defense Security & Technology Inc (IDST). 2020. ‘3D printing to enable on-demand, 3D-printed explosives at the front line’. <https://idstch.com/military/3d-printing-to-enable-on-demand-3d-printed-explosives-at-the-front-line/>.
Jenzen-Jones, N.R. 2015. ‘Small arms and Additive Manufacturing: An assessment of 3D-printed firearms, components, and accessories’ in: King, B. & G. McDonald (eds.). Behind the Curve: New Technologies, New Control Challenges. Geneva: Small Arms Survey. <http://www.smallarmssurvey.org/fileadmin/docs/B-Occasional-papers/SAS-OP32-Behind-the-Curve.pdf>.
Jenzen-Jones, N.R. & J. Ferguson. 2018. ‘Weapons Identification: Other Small Arms and Light Weapons’ in: Jenzen-Jones, N.R. & M. Schroeder (eds.). An Introductory Guide to the Identification of Small Arms, Light Weapons, and Associated Ammunition. Geneva: Small Arms Survey. <http://www.smallarmssurvey.org/resources/publications/by-type/handbooks/weapons-id-handbook.html>.
Machine Design. 2018. ‘A Look Inside the “Explosive” 3D-Printing Industry’. <https://www.machinedesign.com/3d-printing-cad/article/21836373/a-look-inside-the-explosive-3dprinting-industry>.
Popular Science. 2014. ‘U.S. Army Contemplates 3D-Printed Warheads’ <https://www.popsci.com/article/technology/us-army-contemplates-3d-printed-warheads/>.
Purdue University. 2017. ‘Purdue University Energetic Materials and Additive Manufacturing’. Presentation: 17 August. <https://www.slideshare.net/MikeDodd17/purdue-university-energetic-materials-and-additive-manufacturing>.
Purdue University. 2019. ‘3D Printing Energetic Materials’. YouTube video: 4 February. <https://www.youtube.com/watch?v=o9W-8FNvbCs>.
Remember, all arms and munitions are dangerous. Treat all firearms as if they are loaded, and all munitions as if they are live, until you have personally confirmed otherwise. If you do not have specialist knowledge, never assume that arms or munitions are safe to handle until they have been inspected by a subject matter specialist. You should not approach, handle, move, operate, or modify arms and munitions unless explicitly trained to do so. If you encounter any unexploded ordnance (UXO) or explosive remnants of war (ERW), always remember the ‘ARMS’ acronym:
AVOID the area
RECORD all relevant information
MARK the area from a safe distance to warn others
SEEK assistance from the relevant authorities