Kristóf Nagy & Paulos Skontzos
Riot control agents (RCA)—colloquially described as ‘tear gas’—were introduced to the Hellenic Police in the 1960s, following the experience of members of their designated riot control units, Monades Apokatastasis Taksis (‘Units for the Reinstatement of Order’; MAT), who experienced the potential of such agents during training courses in the United States. Since then, the utilisation of RCA became widespread within Greek law enforcement, encompassing delivery methods from hand-thrown grenades to projectiles fired from low-velocity launchers. Despite a significant domestic demand which has grown over the decades, almost all RCA munitions have been sourced from the international market. In fact, there is no domestic production of less-lethal devices in Greece at present.
This stands in stark contrast to the robust explosives, hand grenades, and ammunition manufacturing capabilities developed by the Greek defence industry. Much of this was led by Elviemek, a Greek ordnance company founded in 1960, and known for their production of hand grenades and land mines. For decades, Elviemek supplied the Greek military with a range of fragmentation and smoke grenades designed around a common fuze assembly. According to Greek sources, there was an effort made during the 1980s to design and develop a domestically produced RCA grenade.
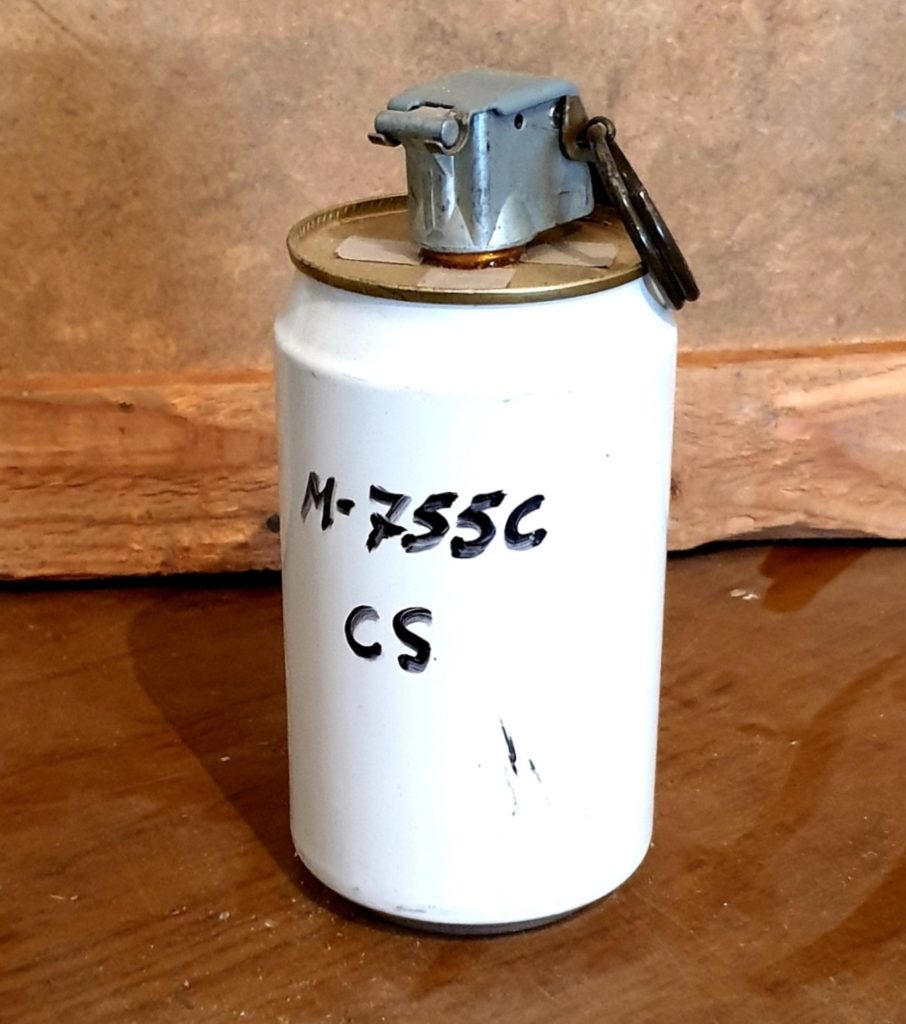
The Elviemek prototype (see Figure 1.1) appears to be the result of that programme. The most prominent feature of this design is the utilisation of what appears to be a carbonated beverage container (‘soda can’) as the grenade body. Whilst this may be puzzling at first impression, there are some sensible reasons why such a design might have been chosen. The mass production of drink cans was commonplace in Greece at that time, offering an extant, proven, and accessible technology from which to develop a new product. The technology used for filling aluminium cans with pressurised beverages also matched, in many respects, that required to process RCAs in a safe way during production. Using a well-established process that provided a fast, cheap, and leak-free filling and sealing capability clearly struck the engineers at Elviemek as the ideal solution for manufacturing a small lot of pre-production prototype grenades.
The spray-coating process used to coat the inside of beverage cans with an epoxy lacquer is industry-standard, and this provided a barrier layer which helped prevent the 2-chlorobenzalmalononitrile (CS) fill and other filling materials from causing corrosion which may result in leakage. The dome-shaped bottom of a standard drink can—designed to help withstand the pressure of carbonated beverages—also helped maintain the structural integrity of the RCA device, resulting in a controlled dispersal of CS particles and smoke once the device was ignited. Ignition was achieved using the same fuze assembly (with classic ‘spoon’ fly-off lever and pull-pin safety mechanism) already used on the Greek EM-series of fragmentation and smoke grenades. CS is believed to be the only chemical fill tested by Elviemek in these prototype grenades.
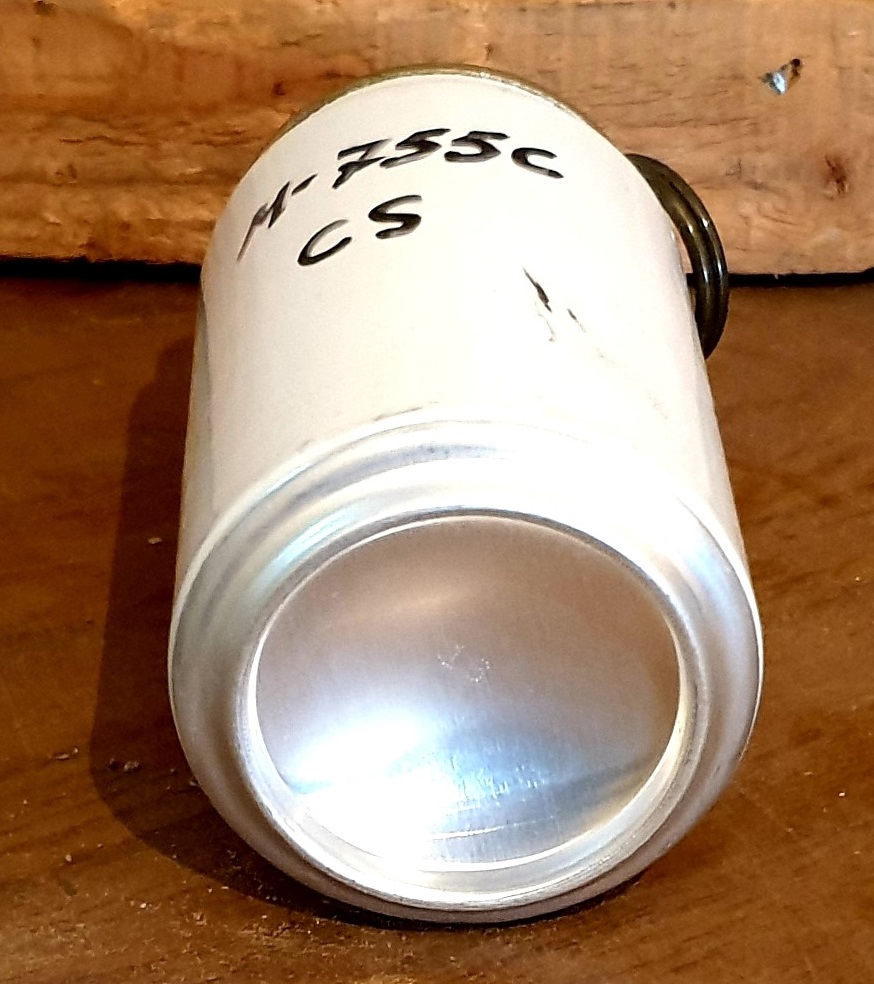
Despite what would seem a promising business opportunity, given Greece’s domestic demand for RCA munitions, the project was ultimately a dead-end. The Elviemek prototype CS grenades underwent testing from 1989 to 1991, but never made it into serial production. The ‘soda can’ approach likely provided a perfectly viable prototype, but is unlikely to have been suitable for serial production. There may have been safety concerns with the relatively thin walls of the beverage container body, however the filler material appears to provide additional rigidity and the munition is surprisingly ‘solid’ when handled. With improvements to the design, and with proper financial backing, a refined version of this munition would have provided an interesting business opportunity for Eviemek to break into the sizeable Greek market. A key reason for the lack of further development could be the desolate financial situation Elviemek experienced in the 1990s. Regardless of the reasons for its failure, what is left is a fascinating prototype which combines key production technologies from different industrial sectors to produce a unique munition.
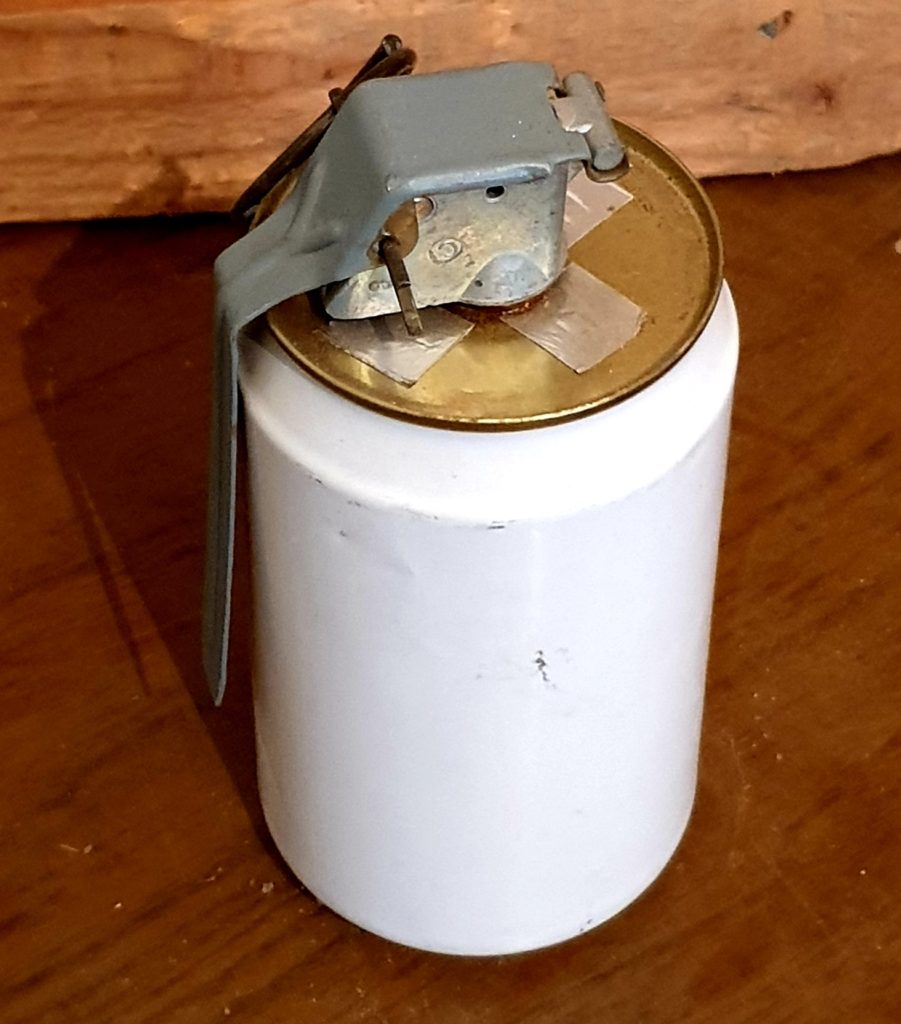
Sources
Hellenic Police. 2003. Regulations on the Organisation and Tactics of Riot Police Operations. Athens: Hellenic Police Headquarters.
Small Arms Survey. 2001. ‘Small Arms, Big Business: Products and Producers’ in Small Arms Survey 2001. Geneva: Small Arms Survey.
Yam, K. L. 2009. Encyclopedia of Packaging Technology. Hoboken, NJ: John Wiley & Sons.
Remember, all arms and munitions are dangerous. Treat all firearms as if they are loaded, and all munitions as if they are live, until you have personally confirmed otherwise. If you do not have specialist knowledge, never assume that arms or munitions are safe to handle until they have been inspected by a subject matter specialist. You should not approach, handle, move, operate, or modify arms and munitions unless explicitly trained to do so. If you encounter any unexploded ordnance (UXO) or explosive remnants of war (ERW), always remember the ‘ARMS’ acronym:
AVOID the area
RECORD all relevant information
MARK the area from a safe distance to warn others
SEEK assistance from the relevant authorities